Ausfälle voraussagen mit KI, IoT und Sound
Smarte Datenanalyse
Die Datenerfassung ist jedoch nur der erste Schritt. Als Nächstes müssen nützliche Daten extrahiert und analysiert werden. Dafür werden häufig Machine-Learning- und Deep-Learning-Methoden eingesetzt. «Das Hauptziel dieser Phase ist, ein Muster in Audiodaten zu erstellen, mit dem verschiedene Arten und Bedingungen des Maschinenbetriebs automatisch unterschieden werden können», erklärt Kristina Paralidis. Eine wichtige Grundlage sind dabei die Daten des gesunden Zustands gleicher Maschinen und Anlagen, die unter den gleichen oder sehr ähnlichen Bedingungen laufen.
Damit die KI-Modelle alle auftretenden Geräusche eigenständig korrekt identifizieren können, muss eine umfassende Datenbank von Fehlergeräuschen realer Anlagen und Maschinen vorhanden sein. «Mehr Daten, die unterschiedliche Fehlerzustände der seltenen, atypischen und einzigartigen Betriebsarten darstellen, würden mehr Wissen bringen und bestehende Methoden für die vorausschauende Wartung verbessern», so Paralidis. Deshalb erfordert die erste Phase der Implementierung oft einen menschlichen Input. Die erfahrenen Techniker müssen die auftretenden Geräusche teilweise zuerst selbst bewerten und kennzeichnen.
Sollte es dabei an ausreichend Datensätzen mangeln, können auch andere Methoden angewandt werden. So analysiert innSono auch begrenzte Mengen an Fehlerdaten umfassend und unterstützt KI-Modelle, indem bedeutsame Teile der Audiosignale hervorgehoben werden. Darüber hinaus werden Data-Engineering-Verfahren angewandt, für die nicht zwingend grosse Mengen an Fehlerdaten erforderlich sind. Kristina Paralidis nennt als Beispiel «Techniken, die auf eine autonome Anomalien-Erkennung in einem Datensatz abzielen, wenn diese auftreten, und nicht versuchen, unbekannte Daten in eine der vordefinierten Gruppen zu klassifizieren».
Neuron Soundware wiederum hat sich intensiv mit unterschiedlichen Methoden zur Datenergänzung befasst. Die Überlegung dahinter: Wenn es nicht genügend Fehlerdaten gibt und diese nicht simuliert werden können, dann müssen sie künstlich erzeugt werden. «Wenn die Menge solcher Proben gross genug ist, ist die Messgenauigkeit unter realen Betriebsbedingungen in den meisten Fällen tatsächlich recht gut», konstatiert Martin Kuban.
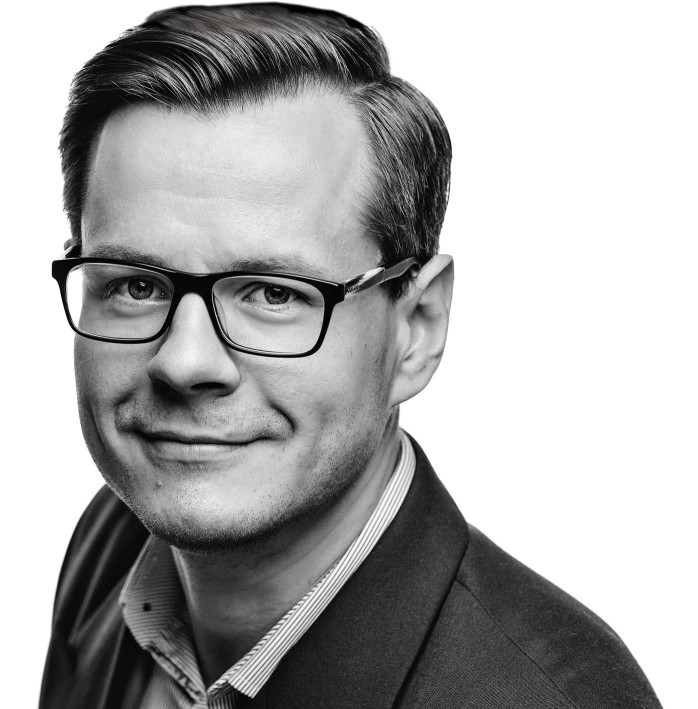
“Sound ist viel mehr als das, was das menschliche Ohr wahrnimmt.„
Kai Saksela, CEO und Mitgründer von Noiseless Acoustics
Auch wenn der Implementierungsaufwand in der Anfangsphase als ziemlich hoch erscheint, können die künftigen Einsparungen es wert sein, wie das Beispiel von Anheuser-Busch InBev zeigt. Der Konzern, bekannt für seine Biermarke Budweiser, wollte testen, ob mittels drahtloser Sensoren, die Ultraschallgeräusche erfassen, vorhergesagt werden kann, wann Maschinen gewartet werden müssen. Im Rahmen dieses Projekts wurden 20 drahtlose Sensoren an drei Motoren der Verpackungslinie installiert. Die aufgenommenen Geräusche wurden mit den Geräuschen eines «gesunden» Motors verglichen, die als Basis für die KI-gestützte Anomalie-Erkennung dienten.
Nach eigenen Angaben hat die Installation der Sensoren im Werk in Fort Collins 20.000 Dollar gekostet - und seit ihrer Bereitstellung ausserplanmässige Unterbrechungen der Produktionslinie sowie Produktverluste von mehr als 200.000 Dollar verhindert. Deshalb plant der Konzern, weitere Brauereien in allen sechs globalen Regionen, in denen er tätig ist, mit den Ultraschallsensoren auszustatten.